In occasione del progetto “Open Factory" molti centri di eccellenza veneti hanno aperto le proprie porte al mondo esterno nel fine settimana: una mano tesa al territorio, affinché cittadini e realtà produttive potessero conoscersi, stringersi la mano, fare conoscenza. C’è qualcosa oltre lo storytelling e poter vedere con i propri occhi significa vidimare la narrazione che i brand fanno di sé stessi nel mondo esterno. Abbiamo partecipato al progetto aggregandoci alla grande carovana di visitatori che ha scelto lo scenario di Venezia e delle raffinerie Eni, uno dei punti di massima innovazione per il gruppo. Perché nelle raffinerie venete non c’è soltanto una immagine da svecchiare: l’impianto è stato profondamente riprogettato e raccontarne la conversione ai cittadini diventa un approccio dialogico che i presenti hanno dimostrato di apprezzare.
Grazie ai punti nevralgici di Versalis e della Raffineria di Venezia, Eni ha calato sul territorio due assi che hanno saputo portare sul suolo delle città veneta una realtà invidiata in tutto il mondo in termini di innovazione e qualità produttiva. Grazie agli investimenti del gruppo, Venezia è diventata oggi una delle realtà più avanzate nel settore della chimica e nella produzione di carburante green e di questo ne ha beneficiato anche l’intero indotto economico e sociale grazie ai nuovi posti di lavoro che hanno salvato un territorio che con la crisi del 2011 era in forte difficoltà.
La riconversione è una opportunità sotto molti punti di vista, quindi: un prodotto più sostenibile in uscita, un procedimento che diventa proprietà intellettuale di grande prestigio e un contesto che migliora le condizioni di lavoro offrendo maggiori garanzie di occupazione.
Versalis, controllata Eni, offre al mercato un ampio portafoglio costituito da circa 400 prodotti e una nuova gamma di intermedi chimici ottenuti da materie prime rinnovabili. Tra i prodotti si menzionano l’etilene, il propilene, il C4 mix, il benzene, il toluene ed il DCPD. L’infrastruttura è imponente e si compone di una rete stradale interna di 40 km, una rete ferroviaria interna di 12 km, 5 pontili ed una pipeline di collegamento con Mantova, Ferrara e Ravenna (tot. circa 400 km) per trasporto Monomeri e Intermedi. Attualmente una parte dell’infrastruttura di Versalis di Venezia è in fase di rammodernamento, lo stabilimento può contare su un impianto di Cracking per la produzione di olefine, un impianto CR 20-23 per la produzione di aromatici, una centrale termoelettrica per la produzione e distribuzione di vapore ed energia elettrica in cogenerazione ed una struttura di logistica per il ricevimento, stoccaggio, spedizione, di materie prime e prodotti finiti in conto proprio e per terzi.
La lavorazione di un prodotto segue il seguente iter: via nave arriva la Virgin Nafta che viene scaricata e stoccata in appositi serbatoi e poi viene trasferita agli impianti di produzione olefine e aromatici; tutti i prodotti chimici realizzati vengono poi elaborati, differenziati e spediti per la produzione di tutti quegli oggetti che li contengono.
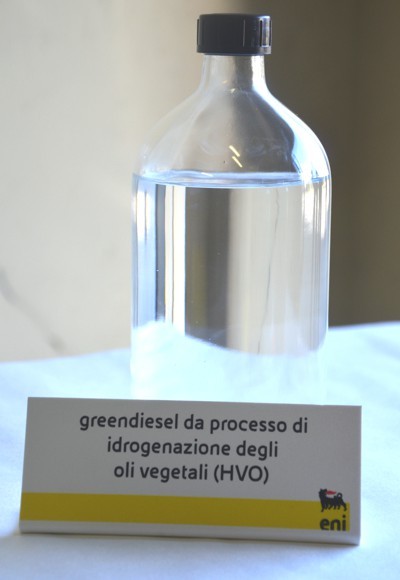
Green diesel, componente bio di Eni Diesel +
Ma il futuro di Versalis è anche, e soprattutto, green. L’olio vegetale è sostanzialmente una miscela di lipidi ricavata principalmente da frutti e semi oleosi le cui caratteristiche dipendono dalla pianta di origine, dalle condizioni specifiche di coltura e dalla qualità del seme. Versalis, con la collaborazione di Elevance Renewable Sciences, sta ingegnerizzando un progetto per la realizzazione a Porto Marghera di un polo tecnologico le cui future produzioni saranno destinate a settori applicativi ad alto valore aggiunto quali cura della persona, detergenti, bio-lubrificanti e prodotti chimici per l’industria petrolifera.
Green Diesel
La Raffineria di Venezia dispone di un primato unico al mondo ed è quello di essere il primo esempio di riconversione di una raffineria tradizionale in bioraffineria, un luogo in cui si trasformano materie prime di origine biologica in biocarburanti di alta qualità. All’interno di questo luogo Eni produce green diesel, green nafta, GPL e potenzialmente anche jet fuel. Attualmente lo stabilimento è alimentato da olio di palma, ma in futuro è previsto l’utilizzo anche di biomasse non in competizione con gli usi alimentari. Cuore tecnologico del progetto è Ecofining, sistema sviluppato nei laboratori di San Donato Milanese in collaborazione con Honeywell-UOP e poi applicato alla sezione catalitica di idrodesolforazione della raffineria di Venezia. Lo stesso Ecofining ha permesso di intraprendere anche un’altra ambiziosa sperimentazione e cioè l’alimentazione a biodiesel del pattugliatore d’altura Foscari della Marina Militare italiana, primo esempio di questo tipo a livello mondiale.
Lo scenario che ha portato Eni a questa riconversione è da ricercarsi in tre fattori: la crisi del 2011 del settore delle raffinerie, le nuove Direttive Europee sui biocarburanti e le nuove opportunità derivanti della tecnologia Ecofining. La riconversione è stata incentivata anche dall’enorme risparmio economico e di tempo ottenibile partendo da una raffineria già esistente. In soli 6 mesi di tempo, infatti, la vecchia raffineria è stata trasformata in una bioraffineria.
Ma la Raffineria di Venezia non è oggi per Eni un punto di arrivo, quanto piuttosto un punto di partenza. Per il triennio 2017-2020 si punta, infatti, ad incrementare la capacità produttiva e la flessibilità dell’impianto. I vantaggi di realizzare un carburante green, come il green diesel, cioè quello che alla pompa è chiamato “ENI Diesel+” sono molteplici. Innanzitutto, grazie alla maggiore qualità del carburante, con il 15% di componente rinnovabile (e grazie, dunque, alla maggiore efficienza nella combustione del motore) è possibile ottenere una riduzione dei consumi del 4%, ridurre le emissioni gassose fino al 40% e ridurre la CO2 in media del 5%.
Innovazione in tutta sicurezza
Innovazione, un futuro green, ma non solo. Perché tutte queste eccellenze non sarebbero possibili in aziende rispettose del territorio e con ampie garanzie di sicurezza. I sistemi di controllo tri-ridondanti ed il costante monitoraggio attento dalla cabina di controllo fanno si che nulla possa succedere. Ma nella remota ipotesi che qualcosa non dovesse funzionare, la presenza in loco di una stazione dei vigili del fuoco fa si che gli interventi avvengano in meno di due minuti. Per affinare le tecniche di sicurezza, ogni settimana i vigili del fuoco compiono 4 esercitazioni ed ogni anno, per 6 volte, l’intero staff della raffineria compie un’esercitazione di sicurezza.
La visita agli impianti ha consentito di vedere i lavori in corso e le esercitazioni per la sicurezza degli impianti. I visitatori sono stati accompagnati in questo tour avendo la possibilità di dialogare con i responsabili dell’impianto, dando vita ad un dialogo fatto di conoscenza e di proiezioni al futuro. Open Factory ha aperto le porte e così facendo ha consentito l’incontro tra due parti che hanno assoluto bisogno di conoscersi a vicenda. Per il bene di tutti.